CLOUD COMPUTING APPLICATION CASE STUDY: VELTEK ASSOCIATES, INC.
Veltek automates tracking, tagging and scanning processes for increased productivity.
ABOUT VELTEK ASSOCIATES, INC.
Veltek Associates, Inc. designs innovative solutions to address the control of particulate and microbial contamination in pharmaceutical and biotechnology operations worldwide.
VAI strives to develop meaningful technical relationships with our clients to ensure that VAI products meet, if not exceed, their unique requirements. The products from VAI’s four divisions build upon each other, making the company a full-circle, single-source supplier able to address any pharmaceutical or biotechnology contamination control requirement.
VAI has been an industry leader since 1981 and has over 135 US and International Patents. We are committed to continual innovation and improvement in our products to satisfy current and future regulatory requirements. Our corporate capabilities and pharmaceutical experience provide the framework for continuing VAI’s leadership in contamination control.
THE CHALLENGE
Automate tracking the location of prohibitively expensive devices as they move across large campuses, from lab to lab.
VAI and its customers operate in a highly controlled environment that requires constant air-quality and surface-sterility monitoring. Within this sterile environment, sealers, precision scales, high-end cleaning devices, and equipment carts are used to ensure pharmaceutical regulations are met. Additionally, they’re subject to strict operating procedures around their introduction into the lab environment, calibration, and preventive maintenance.
“Customers were spending an enormous amount of time just trying to locate the equipment, which caused them to use twice as many resources as needed.”
— Doug Paradis, Veltek CTO
Tracking the location of these prohibitively expensive devices as they move across large campuses, from lab to lab, proved to be a very difficult process. Machines would often be misplaced for long periods of time, causing them to miss critical maintenance procedures. In some worst-case scenarios, devices failed to be located and were lost altogether. VAI realized the industry needed a way to easily track and locate equipment, as well as to automate the documentation process and eliminate manual Excel procedures.
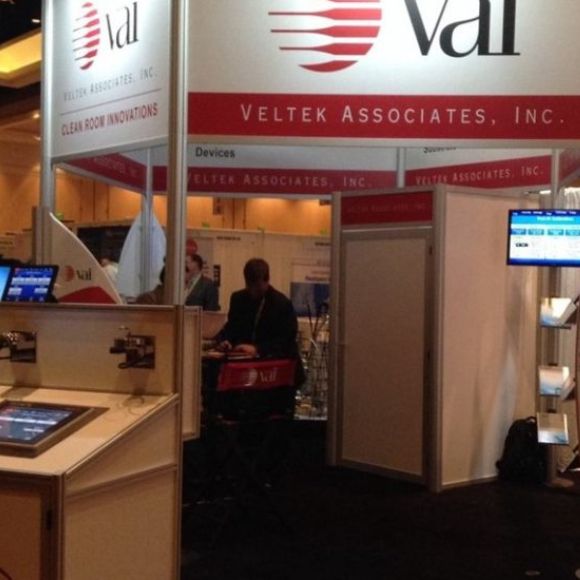
“Verinext did an outstanding job through the entire process to manage priorities and develop the application features. Teams from both organizations worked closely together to make sure we were building a compliance-based solution that met all of our needs.”
– DOUG PARADIS, VELTEK CTO
THE SOLUTION
Verinext delivered a computer-based and web-based application which provided RFID tracking, tagging, and scanning—including support by a cloud-based infrastructure.
To automate their processes, alleviate compliance issues, and minimize the frustration and time wasted tracking down missing equipment, VAI chose to partner with Verinext on the digital components of the overall solution.
Veltek devised the Core2Scan system, a hardware and software solution to track the physical location of mobile assets (machines) and automate the maintenance-documentation process. Veltek chose Verinext as a key partner for the computer-based and web-based application which provided RFID tracking, tagging, and scanning—including support by a cloud-based infrastructure.
RFID tags placed on mobile equipment send signals to a scanner which, in turn, sends “check-in” and “check-out” information to a data hub in the cloud. This process is tracked to a facility map that records and displays the exact location of each machine within the cloud computing application.
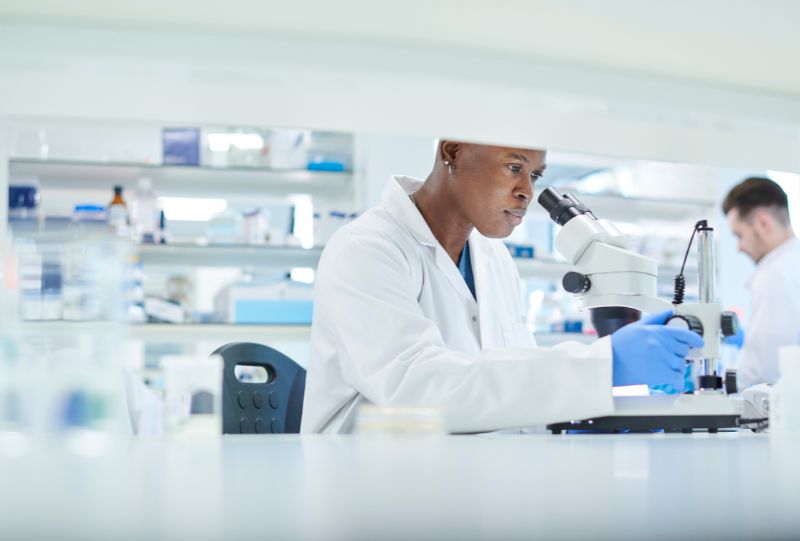
THE RESULTS
The Verinext Core2Scan system delivers automation for relevant scheduling to ensure equipment accountability.
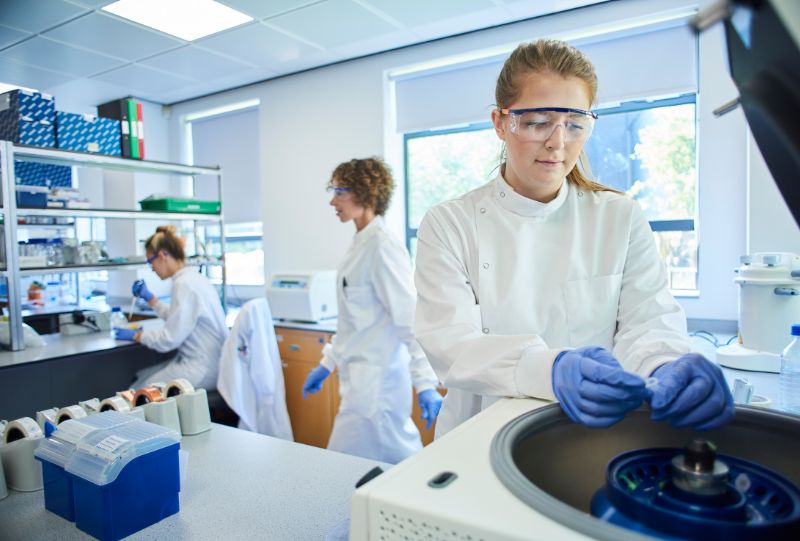
The net result was the creation of an RFID tracking system and automated maintenance documentation process that could also be white-labeled and sold to VAI’s customers.
There’s no margin for error when it comes to clean rooms and lab environments. Ensuring accountability and cleanliness—as well as documenting machines are functioning properly, and guidelines are followed—is paramount. To ensure these criteria are met, Core2Scan alerts users whenever a piece of equipment needs recalibration, then automatically updates the relevant scheduling and documentation via the cloud.